一.高压电缆国产化趋势及国内市场的前景分析
电力电缆是电线电缆工业中一个重要的组成部分,在电力电缆领域内:1~10kV属于低压电缆、10~35kV属于中压电缆、110~220kV属于高压电缆、500kV属于超高压电缆。
国外从二十世纪七十年代开始生产高压交联聚乙烯电力电缆,目前国外超高压交联聚乙烯绝缘塑料和超高压交联聚乙烯绝缘电缆能够达到500kV以上的耐压等级。国外超高压聚乙烯绝缘电缆已经非常成熟并建立了从聚乙烯基料、高压交联聚乙烯绝缘塑料到高压交联聚乙烯电缆的完整体系.
我国的电线电缆工业相对起步较晚,但是发展迅速。自1991年正式国产以来通过17年多的积累和发展,除超高压等级外我国高压电力电缆制造已经相当成熟,国产高压交联电缆已建立完善评价体系,17年多的实际运行情况已经证明我国高压电力电缆具有高稳定性。
以我国现在的电缆市场行情,行业需求的发展趋势所向,当务之急是提高电缆的科技含量,提高技术水平,实现产品结构的高端化。110KV及以上的高压交联电缆是我国目前电线电缆的急需品种。
此外,国家“十一五”期间国家的能源政策将发生一些重大变化,合理解决国家电力资源不平衡问题和总体降低电缆运行成本将成为“十一五”主题之一,特别是金融风暴之后,政府拉动内需计划中的基础设施建设可能会提前,这些变化将给我国高压交联电力电缆带来巨大的发展机遇。
在生产装备、市场和机遇都具有的前提下,大力发展国产高压电缆品种有以下几个意义:
1.改变我国低端低利产品富裕,中高级产品缺乏的现状;
2.完成国产电缆升级换代和企业结构调整;
3.把整个高压电缆产业链实现国产化作为一个拉动内需的有效手段。
二.高压电缆用绝缘料国内市场的前景预测
我国高压交联电力电缆使用量的急剧增加必将带动高压交联聚乙烯绝缘料市场的快速发展。我们依据高压交联电力电缆的市场的发展需要对我国高压交联聚乙烯绝缘料做了一个预测如下:
表1 高压交联聚乙烯绝缘市场预测
年份 |
高压交联电缆
总量(千米) |
高压交联电缆
产值(亿元) |
高压交联绝缘料
用量(吨) |
2004 |
3500 |
14 |
10000 |
2005 |
4500 |
18 |
12500 |
2006 |
7000 |
28 |
22500 |
2007 |
10000 |
40 |
28000 |
2008 |
12000 |
48 |
33500 |
2009 |
15000 |
60 |
42000 |
2010 |
18000 |
72 |
50000 |
三.高压电缆用绝缘料技术特性分析
我们收集了国外同类产品说明书及实样,并同现有的国产中压绝缘料进行了性能比对,同时还收集了高压电缆国家标准GB/T11017.1-2002附录对材料要求(具体见表2),并分析了IEC国际电工委员会标准和国家高压电缆标准,有关数据详见表3:
表2 国内中压电力电缆用可交联聚乙烯塑料与高压电缆国标
及国外高压产品性能实测值对照表
指 标 名 称 |
计量单位 |
高压电缆
国家标准附录 |
国外高压产品 |
国内中压产品 |
1.20℃体积电阻率 |
≥1.0×1015 |
5.0×1016 |
6.5×1016 | |
2.介电强度50 Hz |
kV/mm |
≥22 |
34 |
35 |
3.介电常数50 Hz |
|
≤2.35 |
2.30 |
2.30 |
4.介质损耗因数50 Hz |
|
≤5×10-4 |
0.0003 |
0.0003 |
5.拉伸强度 |
MPa |
≥17 |
21.2 |
19.6 |
6.断裂伸长率 |
% |
≥500 |
496 |
518 |
7.热延伸试验
试验温度
载荷时间
机械压力
载荷下最大伸长率
冷却后最大永久伸长率 |
%
% |
200℃
15min
0.2MPa
≤100
≤10 |
200℃
15min
0.2MPa
50
2 |
200℃
15min
0.2MPa
52
1 |
8.凝胶含量 |
% |
≥82 |
82 |
85 |
9.杂质含量≥100μm |
个 |
0 |
0 |
2 |
表3 国际电工委员会IEC标准和国家高压电缆标准电缆要求对照表
序号 |
项 目 |
单位 |
GB/T 11017.2-2002 |
IEC 60840-1999 |
1 |
密度(23℃) |
|
0.922±0.002 |
0.922±0.002 |
2 |
老化前抗张强度 |
MPa |
≥17 |
≥17 |
3 |
老化前断裂伸长率 |
% |
≥500 |
≥500 |
4 |
热延伸试验
(200℃,0.2MPa,15min)
载荷下最大伸长率
冷却后最大永久伸长率 |
%
% |
≤100
≤10 |
≤100
≤10 |
5 |
凝胶含量 |
% |
≥82 |
≥82 |
6 |
介电常数 |
|
≤2.35 |
≤2.35 |
7 |
介质损耗因数 |
|
≤0.0005 |
≤0.0005 |
8 |
介电强度 |
|
≥22 |
≥22 |
9 |
体积电阻率(23℃) |
Ω.m |
≥1.0×1014 |
≥1.0×1014 |
10 |
杂质水平 |
|
杂质含量≥100μm
0颗 |
杂质最大尺寸
(1000g样片中)
≤0.10 mm |
从这些数据比对我们可以看出:高压电缆用绝缘料与常规中低压绝缘料相比,其关键在于杂质水平的提高,这个提高主要体现在两个方面:一是杂质的最小尺寸要求变小,下表列出了国家电缆标准对于电缆用材料杂质的要求;二是杂质种类要求的变化,高压电缆用绝缘料要求控制凝胶的大小。具体如下:
表4 高压交联聚乙烯绝缘与中低压交联聚乙烯绝缘要求比对表
项 目 |
高压绝缘料 |
中低压绝缘料 |
原料熔融指数 |
2.0±0.1g/10min |
2.0±0.1g/10min |
凝胶、杂质 |
等同处理 |
重点控制杂质 |
原料产品稳定性要求 |
非常高 |
高 |
最大杂质尺寸 |
≤0.10 mm |
≤0.125mm |
以上我们可以看出高压电缆用聚乙烯基料至少满足最大杂质尺寸必须小于0.10mm要求,但目前我们的聚乙烯基料还达不到这个水准。国标中提出的这个要求仅仅是高压交联绝缘料的基本要求,从我们对国外产品的研究我们可以知道:国外高压交联绝缘料相对我们目前的产品主要在电性能、杂质水平、杂质种类、聚合物分子量的稳定性方面有大幅度的提高。目前国外能够达到的水平如下(7-10为明显提高项目):
表5 国外当前高压聚乙烯聚乙烯绝缘塑料水平(可用于220KV高压电缆)
序号 |
项 目 |
单位 |
性能指标 |
1 |
密度(23℃)(基料) |
kg/m3 |
0.922±0.002 |
2 |
老化前抗张强度(250±50mm/min) |
MPa |
≥17 |
3 |
老化前断裂伸长率(250±50mm/min) |
% |
500 |
4 |
热延伸试验(200℃;)
负荷伸长率
永久变形率 |
%
% |
≤100
≤10 |
5 |
凝胶含量 |
% |
≥82 |
6 |
介电常数 |
|
≤2.35 |
7 |
介质损耗角正切 tgδ |
|
≤3×10-4 |
8 |
短时工频击穿强度
(较小的平板电极直径25mm:升压速度500V/s) |
kV/mm |
≥25 |
9 |
体积电阻率 (23℃ ) |
Ω·cm |
≥1.0×1017 |
10 |
杂质最大尺寸(1000g的样品中) |
mm |
≤0.05 |
由此可见,对基料和绝缘料杂质的检测和控制是开发高压电缆用绝缘材料的关键。但是净化仅靠杂质过滤和控制是不够的,国产高压绝缘材料若要正真达到国际先进水准,还需要石化企业对高洁净程度基料的开发以及电缆制造企业的支持。高压绝缘材料的国产化离不开上下游企业的通力合作。
四.国产高压电缆绝缘料开发的现状、开发难点及潜在优势
与电力电缆相配套我国国产交联聚乙烯绝缘料虽然也经历了数年的发展,但是目前我国国产交联聚乙烯绝缘料的最高耐压等级仅达到35kV,35kV及以上高耐压等级的交联聚乙烯绝缘料长期被进口产品占据,我国国产高压交联聚乙烯绝缘料的发展完全滞后于高压电力电缆的发展。造成这一现象的主要原因有:
1.我国长期以来中低压电缆市场占据主导地位,对高压电缆产业链缺乏重视和研究。其后果便是高压电缆用绝缘料的技术匮乏,无法与国外的材料竞争。这导致国内电缆厂家在真正需要生产高压电缆的时候,只有依赖进口。在金融危机,外国实行贸易保护的今天,这个问题有可能继续被放大。
2.国内缺乏高净化、稳定的聚乙烯基料,全世界也只有少数几家企业能够提供。聚乙烯基料是发展高压电缆用绝缘料的一个关键问题,拥有超净的高压聚乙烯是高压交联聚乙烯绝缘料产业化的前提。
但是,我们也应该看到,我国拥有广阔的高压电缆市场,一但解决了绝缘料技术上和基料上的问题,对于拉动内需、发展经济乃至促进民族工业的发展都是十分有利的。
五.新上化的高压电缆绝缘料研发思路
作为一个从事电线电缆用材料加工改性多年的企业,我公司有着对中低压电线电缆用绝缘材料丰富的生产经验和优秀的开发团队,早在2006年就开始对高压交联电缆用材料的探索和研究。
不同于中低压绝缘材料,对高压绝缘材料的开发并没有一个可以参照的模式,我们从机理出发,在中压绝缘料的基础上,建立以下的开发思路:
1.用一定的手段去除原料中杂质
2.用杂质检测设备对产品进行中控
3.采取适当的物料输送方式
4.在产品或原料非封闭的区域进行空气净化处理
5.用最终的杂质检测结果决定产品的耐压等级
此外,工艺路线要在中试中确认,装备按研究的结果和设备制造厂共同设计,同主要原料供应商形成同步研究课题,建立对应的品控指标。
对高压绝缘料的生产其实就是一个过程控制,它是把风险留在材料厂家的必然选择。同一工艺、同一设备生产出的产品并不一定全是合格的高压绝缘料,合格的成品最终是测试出来的。
六.新上化的高压电缆绝缘料研发现状
1、杂质检验方法的研究
针对高压电缆用绝缘材料的杂质检测,研究了一套杂质检验方法。采用CCD成像原理在线对用产品挤出的薄带进行线扫描,利用杂质灰度的变化对杂质进行高精度的表征,不仅能够适时反应杂质种类、大小、现状和数量还可以根据检验的结果对产品进行等级归类。原理图如下:
图1 在线杂质检测原理示意图
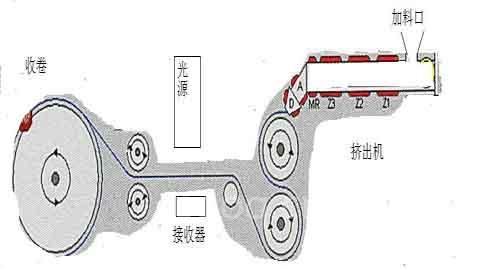
图2 国产某聚乙烯原料杂质检测结果
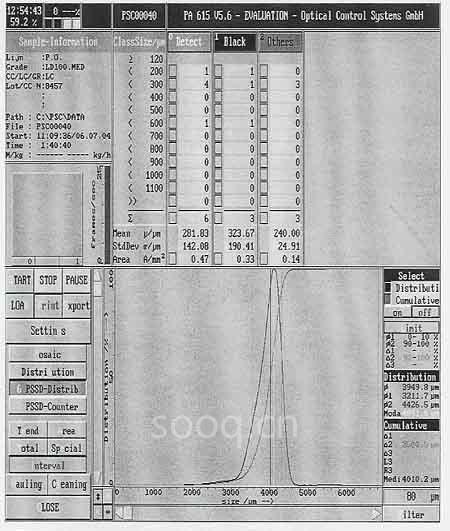
2、杂质类型、生成的原因、去除的方法及全过程的控制研究
杂质类型可细分为杂质、金属和凝胶,生成的原因各不相同,杂质主要存在于基料中,可以用过滤和对基料选择的方式去除,金属主要在物料风送时被引入,去除方法可以从输送方式着手。
(1)过滤工艺
下面是我们采用不同过滤目数滤网对国内某一聚乙烯杂质大小测试结果的一些试验数据:
表6 经过不同过滤网过滤后的杂质检测情况
滤网目数 |
杂质>0.25mm |
杂质0.25~0.125mm |
杂质>0.10mm |
200 |
0 |
5 |
17 |
300 |
0 |
2 |
1 |
400 |
0 |
0 |
0 |
500 |
0 |
0 |
0 |
下面是过滤前后杂质形貌、大小和数量的变化情况,我们可以看到通过我们的过滤设计,杂质个数大大减少,大的聚乙烯凝胶被过滤,这很好的说明了过滤效果。
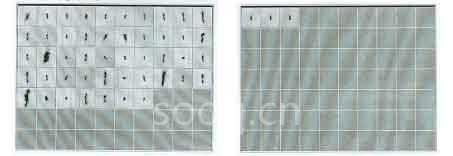
图3 过滤前杂质形貌图 图4 过滤后杂质形貌图
(2)基料选择
杂质去除方法的另外一个途径是对基料的选择,能否获得合适的原料是研制高压电缆绝缘材料的关键之一,通过分析国外产品和原料并与国外原料厂专家进行交流,我们针对高压电缆用绝缘材料提出了下面的要求:
表7 高压电缆用绝缘材料对聚乙烯原料要求
序号 |
项 目 |
单位 |
性能指标 |
1 |
原料密度(23℃) |
|
0.922±0.002 |
2 |
原料熔融指数(190℃/2.16kg) |
g/10min |
2.0±0.1 |
3 |
老化前抗张强度(250±50mm/min) |
% |
≥17 |
4 |
老化前断裂伸长率(250±50mm/min) |
% |
500 |
7 |
介电常数 |
|
≤2.35 |
8 |
介质损耗因数 tgδ |
|
≤3×10-4 |
9 |
短时工频击穿强度
(较小的平板电极直径25mm:升压速度500V/s) |
kV/mm |
≥25 |
10 |
体积电阻率 (23℃ ) |
Ω·cm |
≥1.0×1017 |
11 |
杂质最大尺寸(1000g的样品中)
凝胶 ≥100μm
50~99μm
金属 ≥100μm
50~99μm
杂质 ≥100μm
50~99μm |
颗
|
0
≤20
0
≤4
0
≤8 |
(3)高净化度生产环境
高净化度生产环境是生产高压电缆用绝缘材料的重要条件。根据下表我们可以看出这样的净化级别可以满足高压电缆用绝缘材料实际生产的需要。
表8 净化级别及对应杂质尺寸表(数据来源:ISO 14644-1)
Class |
Number of particles per Cubic Meter by Micrometer size | |||||
|
0,1 mm |
0,2 mm |
0,3 mm |
0,5 mm |
1 mm |
5 mm |
ISO 1 |
10 |
2 |
|
|
|
|
ISO 2 |
100 |
24 |
10 |
4 |
|
|
ISO 3 |
1000 |
237 |
102 |
35 |
8 |
|
ISO 4 |
10000 |
2370 |
1020 |
352 |
83 |
|
ISO 5 |
100000 |
23700 |
10200 |
3520 |
832 |
29 |
ISO 6 |
1000000 |
237000 |
102000 |
35200 |
8320 |
293 |
ISO 7 |
|
|
|
352000 |
83200 |
2930 |
ISO 8 |
|
|
|
3520000 |
832000 |
29300 |
ISO 9 |
|
|
|
35200000 |
8320000 |
293000 |
在我们的中试建设中,对高压电缆用绝缘材料提出了生产环境10000级,包装、送料口1000级的生产环境要求。
(4)物料产品输送
针对金属杂质的问题,我们把风输时物料有可能接触到的金属管道内表面都做了特殊的处理,使其在长期输送作业时,尽可能减少金属杂质的产生。此外,输送用风也经过了几道过滤系统,同样起到了减少杂质引入的作用。
通过杂质去除方法的研究,结合原料、净化和输送我们的获得稳定的过程控制,保证了高压电缆用绝缘材料的低杂质性。
3、配方和工艺技术研究
(1)过氧化物的使用和选择
和中低压电缆用材料一样,对于高压交联电缆用绝缘材料的原料,国内外依然普遍采用具有优良介电性能的聚乙烯,交联的方式则是采取能够给聚乙烯提供均匀高交联度的化学交联方式。
化学交联需要添加过氧化物。过氧化物在添加之前,需要经过沉淀过滤和滤网过滤两道工序。在过氧化物的选择方面,除了常规的性能外,还需要注重过氧化物的半衰期对应温度的关系,我们需要过氧化物能在200到400℃之间的某个温度加速分解,在半衰期对温度的曲线上呈现一个拐点,此类过氧化物对于生产高压电缆有着重要的意义。
高压电缆的绝缘层通常很厚,成缆过程中通过温度梯度变化的硫化管,绝缘层内外层温度不一致,造成成缆后绝缘层内部会出现晶相分离,采用具有某一温度分解拐点的过氧化物,可以使绝缘层在硫化管内交联时有一个缓冲过程,会在内外层达到热平衡后一起交联,从而减少晶相分离的可能,起到防止物理性能降低的作用。
(2)抗氧剂的研究
在化学交联产品加工的整个工艺过程中,抗氧剂的加入量很关键,加的少产品热老化性能不能通过,加的多会使过氧化物的活性降低,对最终形成热固性高分子后,产品的交联度会有影响。我们研究了复配抗氧剂在高压绝缘料中的使用,复配抗氧剂中液体抗氧剂和固体抗氧剂的作用各不相同,相对而言,液体抗氧剂倾向于聚乙烯改性过程中的抗老化,固体抗氧剂倾向于聚乙烯混合物成为制品后的抗老化,两者之间又有协同抗氧化作用。
之所以这么做,是为了在不损失材料交联活性的同时,尽可能的减少抗氧剂的添加量,因为抗氧剂在熔融不完全时扮演了杂质的角色。
(3)加工性能调节
在确定产品交联剂体系以后,我们进行了配方加工性能的研究。对于交联聚乙烯绝缘塑料最重要的加工因素是体系的交联反应活化能和加工流变曲线。我们使用差动热分析仪在氮气的保护下以10℃/min的升温速率研究了不同过氧化物含量体系(按序号递增次序过氧化物含量依次递增)的反应动力学,计算体系反应活化能(E)和一分钟半衰期温度(T1/2)结果如下:
表9 不同过氧化物含量体系的活化能和半衰期
样品
序号 |
活化能 E
kJ /mol |
一分钟半衰期温度
T1/2 ℃ |
1 |
173.4 |
172.8 |
2 |
172.2 |
172.8 |
3 |
170.9 |
171.6 |
4 |
168.1 |
171.3 |
5 |
163.7 |
172.9 |
国外产品 |
164.9 |
171.1 |
我们最终选定了4号配方调节方案,这个配方通过树脂和其它助剂的配合微量调低了过氧化物的加入量,从而微量降低了产品的交联度,改善了过氧化物分解产物对交联电缆产生的不良影响(微孔)。我们还研究了此配方交联流变曲线的硫化时间和平衡扭矩,最终目的使加工性能满足交联聚乙烯电缆的使用要求。
图5 加工性能调节实例
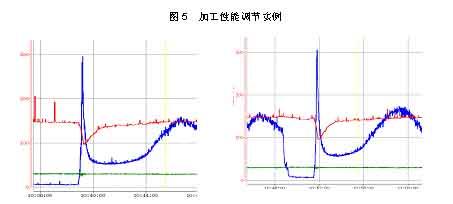
表10 不同过氧化物含量对加工扭矩的影响
过氧化物 Phr |
达到扭矩平衡时最大扭矩 |
达到扭矩平衡时时间 |
达到扭矩平衡时料温 |
2.08 |
20.40 N·m |
7分54秒 |
150℃ |
2.12 |
22.26 N·m |
7分44秒 |
150℃ |
(4)工艺温度控制点的研究
在研究中,我们采用高温工艺先将抗氧剂体系均匀分散在聚乙烯体系中,解决了以往高温长效抗氧剂体系在聚乙烯体系中不熔的问题。接下来采用特殊的工艺使后加工温度从原来的120℃降低到100℃,降低了过氧化物的半衰期,大大降低了过氧化物分解的程度和浓度从而控制了预交联,减少了杂质。
表11 不同温度下过氧化物的半衰期
温度 ℃ |
30 |
100 |
120 |
130 |
160 |
170 |
200 |
250 |
320 |
半衰期 |
490.3年 |
2.1天 |
4.2h |
1.3h |
3.4min |
1.3min |
5.8s |
0.14s |
2.3×10-3 s |
(5)其它工艺控制点的研究
为了保证产品能够稳定生产,确保产品质量稳定我们研究了以下一级工艺控制点。
a.交联剂计量准确性控制点
我们选用高精度体积计量的隔膜泵,并使用失重计量秤对计量系统进行适时计量、反馈调节计量精度,使过氧化物能够平稳、准确加入,整体精度控制在5‰以内。
b.流变曲线测试
作为一种中控的手段,监控产品加工性能。
c.在线杂质检测
在线根据杂质检测结果进行产品分级,对超标情况采用声、光报警并在一定时间后进入自动停车程序。
d.微量水分控制
对原料、中间品和产品进行微量水分测试,避免超标产品在生产高压电缆过程中带来大的微孔,影响电缆电性能。
e.基料过滤压力监控
监控基料过滤前后压力变化情况,对过滤网情况进行监控,超过设定值进行换网。
七. 新上化的高压电缆绝缘料市场合作概念
高压电缆用绝缘材料的开发绝不是靠一两个材料厂家就可以完成的,它需要众多的材料厂家的参与和投入,更需要石化企业和电缆生产企业的关心和支持。新上化诚邀各类合作伙伴的参与,希望在分享交流研发经验的同时,共同协作开发,争取早日实现高压电缆绝缘料的国产化。